The dietary supplement sector has continued to grow strongly since the completion of the good manufacturing practices (GMPs) rules in Malaysia in 2007, in part because of a regulatory framework that permits new products to reach the market quickly. The great variety and accessibility of dietary supplements that encourage a healthy lifestyle have in turn benefited consumers. To ensure that dietary supplements are secure and uphold the high standards that consumers and authorities demand in terms of quality and safety, however, comes a tremendous deal of responsibility with this opportunity and simplicity of the open market. In order to prevent contaminated items from entering commerce, the industry that is engaged in creating dietary supplements and supplementary nutritional products—sometimes referred to differently in other parts of the world—needs to tighten its quality control systems more than ever. By taking these actions, early warning systems for potentially contaminated, adulterated, or subpar raw materials traveling through the supply chain would be created.
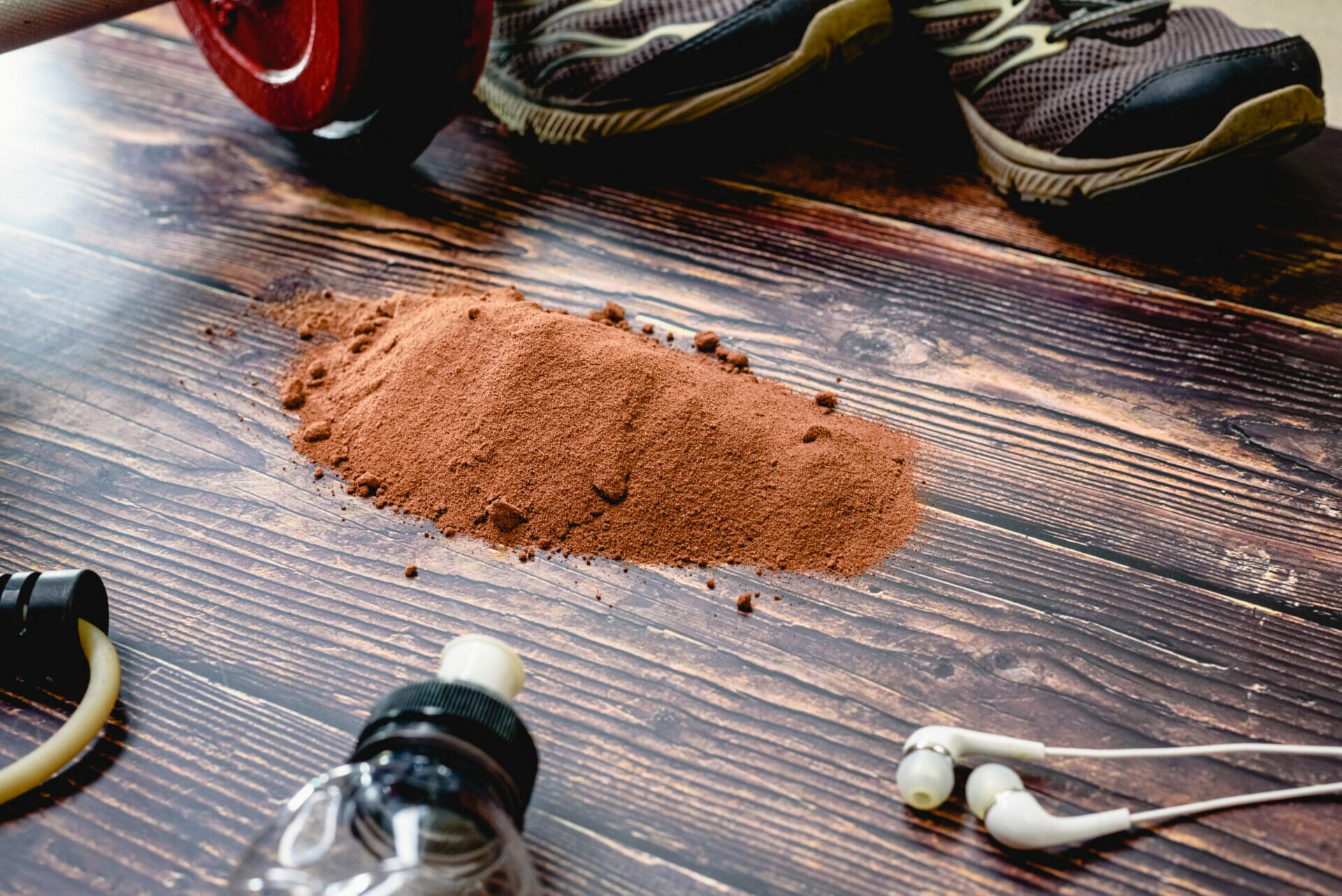
Good manufacturing practices (GMPs)
The requirement for identity testing on all incoming raw material batches ensures that businesses are confirming that the raw materials purchased are actually the intended resources. FDA warning letters and other kinds of communication indicate that many companies are still underinvesting in the creation of suitable test methods to confirm the identity of entering materials. To meet this GMP requirement, many businesses use internal verification technologies, such as Fourier transform infrared (FTIR) spectroscopy and near-infrared (NIR) spectrometers.
These technologies are frequently utilized because they are rapid, affordable, and appealing; however, they might not be suitable for classifying all incoming materials, such as mixes or botanicals. The likelihood that the complexity of the fingerprint will be expected and noticed increases with increasing ingredient complexity. Establishing a reference standard for what a sample of good, high-quality material should look like is the most crucial step; businesses use these reference standards in order to contrast incoming ingredients.
Virtually any substance can be scanned using an FTIR or NIR spectrometer, but without a reference point to measure an item against, it might be challenging to determine whether it fulfills the manufacturer’s requirements. Particularly important when dealing with botanicals, NIR devices are sensitive enough to detect minute variations between different ingredient batches. It is improper to construct reference standards by using a baseline sample of the targeted item for identity verification later; reference standards should instead be independently acquired, qualified, and validated.
Another change brought about by the rule is that businesses can no longer rely solely on the certificate of analysis provided by raw material suppliers (CoA). Companies are required to accept responsibility for the CoA’s accuracy through testing to confirm its accuracy and certify the data against each raw material’s internal specification if dietary supplement firms are going to rely on the information on the CoA, GMPs demand that they qualify their suppliers.
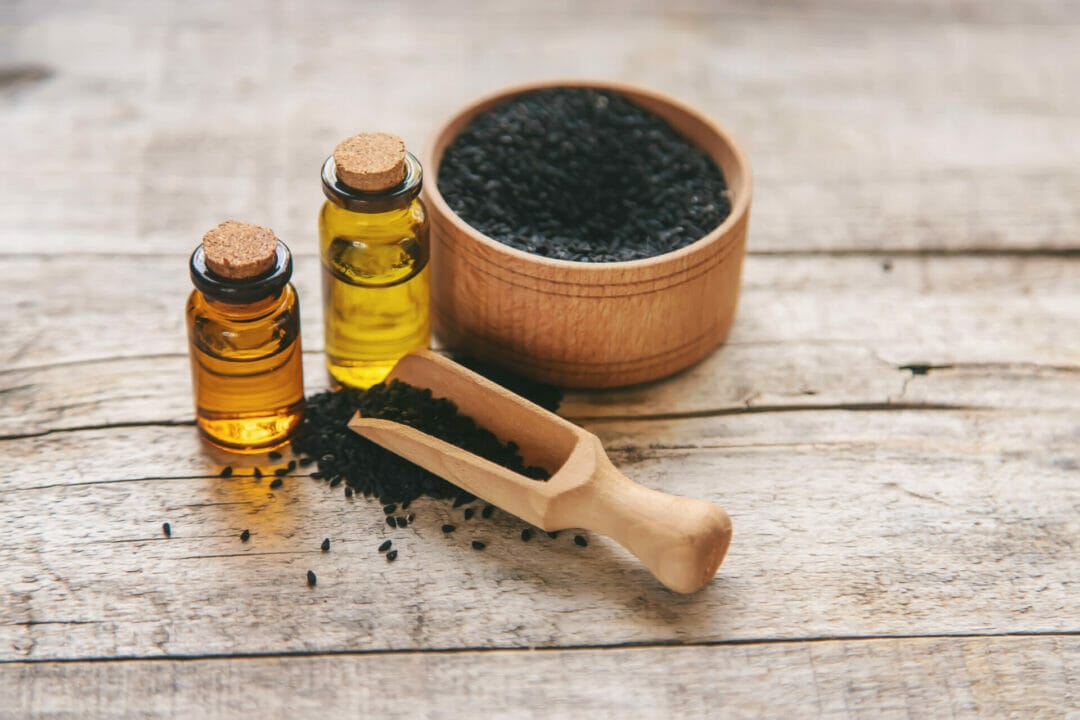
Verification and validation
The distinction between “validation” and “verification” is not always clear to some manufacturers or auditors, and there is significant ambiguity surrounding these phrases. Because of this misunderstanding, it is challenging to fully and successfully implement process controls to make sure the product satisfies quality requirements and maintains ongoing improvement. A HACCP [6] system, for instance, defines verification as “the application of methods, processes, tests and other evaluations, in addition to monitoring to determine compliance with the HACCP plan.” This definition gives examples of specific verification processes, including reviewing procedures or protocols, conducting inspections or examinations, following and passing tests, and reviewing records. In brief, validation seeks evidence that these control measures actually worked and were effective whereas verification focuses that the procedures and controls were applied correctly. Validation may involve some verification steps. Validation is required when direct verification processes, such as in-process and finished product inspection and testing, cannot be adequately carried out to guarantee quality.
Supplier control and the examination or testing of raw materials in accordance with production specifications are typically regarded as one of the most crucial points to control in the manufacturing chain for dietary supplements because any deviation would significantly affect product quality, including the identity, strength, composition, and any potential contaminants. The first step is to establish the needs for the raw materials in accordance with scientific data, legal requirements, and requirements to satisfy the intended use. Before the suppliers of these raw materials are approved, they must first undergo a thorough evaluation that takes into account the qualifying procedure, CoA compliance, the supplier’s quality processes, and other non-quality considerations including supplier history and reputation. Critical production steps, including heating, cooling, weighing, formulation, and particular cleaning and sanitizing activities, must be validated during the manufacture of nutritional supplements in compliance with FDA regulations.
The procedure must be prepared and arranged in advance by skilled and competent professionals for both validation and verification. The tasks should be meticulously carried out in accordance with the specified written processes.
Supplier compliance
A crucial component in the supply chain for dietary supplements and nutritious products is suppliers, especially contract manufacturers. Your product quality and eventually the reputation of your business could suffer if a raw material supplier or contract manufacturer does not adhere to your “quality values.” Supplier compliance should be a crucial component of your quality management system since it ensures that products are made with quality in mind, supporting the idea of quality by design.
To reduce risk to product quality, any supplier who has the capacity to affect quality should be managed in an organized manner. There are three primary components that make up the supplier compliance management process: Choosing a viable provider, keeping track of performance, and conducting frequent on-site evaluations come first.
Either a GMP Questionnaire or an on-site GMP audit should be used to base the assessment. A systematic, impartial, and recorded approach to reviewing particular operations linked to the physical environment, systems, and processes that have an impact on the product is referred to as a quality GMP audit. The audit should specifically confirm the accomplishment of the following goals: (1) Appropriate procedures and systems are in place; (2) processes and systems have been successfully implemented; and (3) processes and systems are effectively followed. The audit’s findings must be sufficiently convincing to demonstrate that the supplier is in line with the desired quality goals.